How My MBA Elevated My Lab Management Skills
Three operational systems I’ve implemented at Sandia National Laboratories
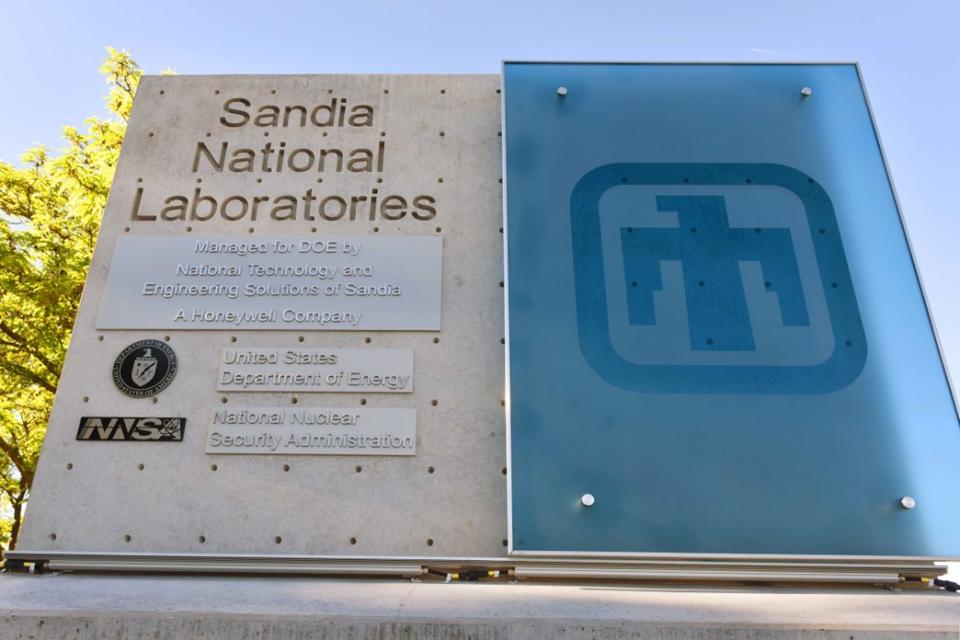
Maintaining a lab can be stressful. There are so many things you have to consider. You have to order supplies, attend meetings, coordinate with customers, and actually do some lab work.
After maintaining a lab for several years as a materials technologist at Sandia National Laboratories, I realized that I needed to get more proficient in managing the space effectively. I enjoyed my work in the lab, but the stress of juggling so many other tasks was getting to be difficult.
After speaking with my manager, I decided that enrolling in the Bay Area MBA program would be a smart decision. I weighed my options carefully and looked at several schools. I was thrilled when I was accepted into the UC Davis program.
Three Operational Systems I’ve Implemented in My Lab
If you are not familiar with Sandia Labs, U.S. national security is our business.
Seen the movie Oppenheimer or know the story? Sandia grew out of America’s World War II effort to develop the first atomic bombs. Today, keeping the U.S. nuclear stockpile safe, secure, and effective is a major part of Sandia’s work as a multidisciplinary national security, engineering laboratory. However, Sandia’s role has evolved to address the additional complex threats facing the nation.
While continuing my work at Sandia, I have been an MBA student for a little over a year. I’ve been able to bring what I’ve learned in the classroom into my lab work. How I operate my lab has drastically changed for the better. The three biggest changes that I have implemented are workflow management, root request analysis, and supply management.
1. Workflow Management
I engage in workflow management through automated systems that allow customers to submit requests and timelines. I can adjust these timelines and apply them directly to my calendar. This helps me plan out the upcoming work weeks and ensure that all deliverables are met on time.
In instances where the timelines are in conflict, I can update customers in real-time to let them know that their deliverables will be met with a small delay.
This simple adjustment has significantly reduced our lab's lead time to customers as well as reduced the amount of stress I personally feel.
2. Root Request Analysis
Root request analysis has been the biggest lifesaver. Otherwise known as the “Five Whys,” this technique mimics what we all did as children: inexhaustibly ask “Why?”
What may have wasted my father’s time then is saving me time now. Asking customers why they need something by a certain date, why they need these specific sets of measurements, and for whom allows me to delve into whether or not they really need the tests done.
It often comes up that these tests were already done earlier, and the legacy data is still valid. They just did not realize that another team had collected it. By addressing their true needs, I save time for both myself and my customers.
3. Supply Management
Lastly, my supply management has improved thanks to the courses offered at UC Davis. I now track how much of certain reagents I use throughout the course of the month. Knowing this allows me to project how much I will likely go through in the coming months.
I can plan out my orders for the year knowing this and set up recurring orders of heavily used materials as a cost-saving measure. Not only does this reduce the price the company pays but it also ensures that I spend less time ordering stock and more time using it.
The perspective offered by the Bay Area MBA program has helped me in many ways. I am thankful for the knowledge that all the professors and staff have shared. I have learned a lot from both them and the other members of the cohort. I am sure that with my last few quarters in residence, I will continue to improve as a lab owner.